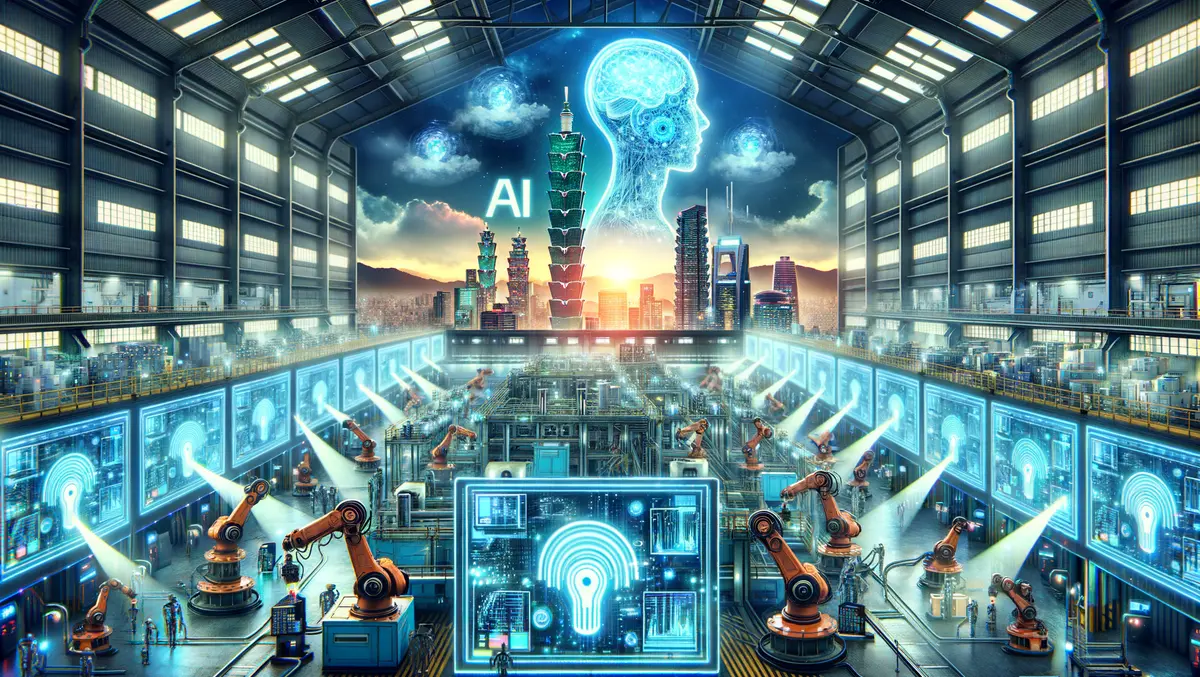
NVIDIA's AI & digital twins transform Taiwanese manufacturing
NVIDIA has announced significant advancements in industrial digitalisation, heralding a new era of autonomous manufacturing for Taiwanese electronics giants. Utilising groundbreaking technologies such as NVIDIA Omniverse, Isaac, and Metropolis, companies like Delta Electronics, Foxconn, Pegatron, and Wistron are revolutionising their factory operations through digital twins and AI-driven workflows.
In his keynote address at Computex 2024, NVIDIA founder and CEO Jensen Huang demonstrated how these companies are leveraging NVIDIA's tools to build highly efficient, digitally integrated factory models. The new reference workflow introduced at COMPUTEX combines NVIDIA Metropolis vision AI, Omniverse physically based rendering and simulation, and Isaac AI robot development and deployment, enabling manufacturers to create and operate digital twins of their factories. These digital twins facilitate real-time simulation of various factory layouts, helping companies optimise space, processes, and efficiency without the need for costly physical changes.
"AI for manufacturing is here. Every factory is becoming more and more autonomous due to the transformational impact of generative AI and digital twin technologies," said Deepu Talla, vice president of robotics and edge computing at NVIDIA. "With NVIDIA Omniverse, Metropolis, and Isaac, the industrial ecosystem can accelerate its adoption of autonomous technologies, helping advance operational efficiencies and lower costs."
Several leading electronics manufacturers are already implementing this innovative technology. Foxconn, one of the largest electronics manufacturers globally, is using NVIDIA Omniverse to develop digital twins of its factories. These digital twins integrate 3D data from industry tools such as Siemens Xcelerator's Teamcenter, allowing Foxconn to optimise equipment layout and monitor worker safety with NVIDIA Metropolis AI cameras. Additionally, Foxconn utilises these virtual environments to simulate, test, and validate autonomous mobile robots (AMRs) and AI-powered robot manipulation arms built on NVIDIA Isaac libraries.
"AI and robotics are poised to revolutionise manufacturing, enhancing safety on factory floors and driving significant operational efficiencies," remarked Young Liu, CEO and chairman of Foxconn. "By integrating NVIDIA Omniverse, Metropolis, and Isaac into our operations, we can create sophisticated digital twins of our factories to train robots, optimising workflows with unprecedented precision and reducing costs."
Delta Electronics, renowned for its electronic and IoT-based smart green solutions, is using NVIDIA Isaac Sim, an extensible robotics simulation platform developed on Omniverse and OpenUSD. This platform generates photorealistic synthetic data for training computer vision models used in its Metropolis-powered automatic optical inspection and defect detection solutions.
Meanwhile, Pegatron is deploying an NVIDIA Metropolis multi-camera workflow and launching services that connect its Omniverse and Metropolis digital twin workflow with NVIDIA NeMo and NVIDIA NIM. This technological upgrade aims to enhance worker safety and productivity across Pegatron's extensively networked factories, which cover over 21 million square feet and produce over 15 million assemblies each month.
Wistron is also benefiting from NVIDIA's technology by building digital twins of its factories to expedite the production of NVIDIA DGX and HGX servers. The company has extended its use of Omniverse to develop digital twins of data centres, ensuring quality, performance, and energy efficiency for newly assembled NVIDIA HGX systems. By simulating its facility and workflows first, Wistron managed to bring its factory online in just two and a half months—halving the typical time required—and increased worker efficiency by over 50% through testing and optimising layouts pre-implementation.
"The combination of NVIDIA Omniverse and NVIDIA Metropolis allows us to test new layouts virtually to identify new processes and monitor real-time operations using live IoT data from every machine on the production line," said Alec Lai, president of global manufacturing at Wistron. "Digitalising our factory planning process has reduced end-to-end cycle times by 50%."
Taiwanese systems integrator Kenmec has also adopted these workflows and services, facilitating their implementation among major manufacturers such as Giant Group. These innovative digital twin workflows are now available as a reference architecture series, promoting widespread adoption across the industrial ecosystem.